Plastic injection molding is a great manufacturing method for prototyping and high-volume production. It is cost-effective and efficient, and it offers superior design flexibility. It also allows manufacturers to meet demanding performance requirements and aesthetic standards.
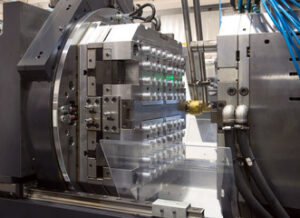
One important design consideration is the wall thickness of your part. It’s best to maintain a uniform thickness, as this promotes consistent cooling and shrinking. It is also recommended to use chamfers and fillets to smooth transitions between sections with different wall thicknesses. Read on Custom Plastic Injection Mold Florida for more information.
Plastic injection molding is a popular manufacturing process used to produce high-volumes of plastic parts and products. The process involves injecting molten material into a pre-machined mold to create the desired product. It is especially useful for companies that need to make large numbers of identical products in a short amount of time. The process also allows for the inclusion of multiple materials in a single piece, increasing versatility and cost-efficiency.
The plastic injection molding process starts with a pellet of raw material that is heated to temperatures above its melting point. The liquid plastic is injected into the pre-machined mold and allowed to cool before it is removed from the tool. This method is ideal for products that require precise control over wall thickness and surface finish. The resulting part is durable, lightweight, and can be finished to the customer’s specification.
Injection molding is a complex process that requires a great deal of precision and accuracy. A poorly designed mold may result in a poor quality product and expensive production costs. To avoid this, Abtec engineers use 3D CAD to review and examine mold designs for flaws. This allows them to identify and eliminate errors early in the design process.
Custom plastic injection molding is a highly versatile manufacturing technique that can be used to create a variety of different types of products and components. It is also an effective way to make prototypes and production parts, making it a great choice for companies that need to produce high-quality products in small quantities.
The process works by injecting a hot liquid of thermoplastic polymer into a pre-machined mold, which is then clamped closed. The molded product is then allowed to set, and once it has solidified, it is removed from the mold with pins. The process can be repeated as needed to create more of the same component.
Injection molding is a relatively low-cost option for companies that need to produce a large number of similar products. The cost of the molds is typically the most significant expense, and this cost can vary widely based on the design of the product. The mold’s complexity, size, and surface finish all affect the final price.
Efficiency
A reliable custom plastic injection molding company will produce complex, precise plastic components with high production efficiency. They will work with you closely throughout the product development process and provide expert guidance to optimize part and mold designs. This will result in a shorter time to market and lower costs for you. Whether you’re looking for a low-volume production of 250 units or high-volume production of more than 1 million parts, you can count on them to deliver quality results.
Injection molding is a high-energy-intensive process, between heating the plastic to its melting point and using powerful injection tools to fill the mold cavities. However, there are several ways to improve energy efficiency in this process, such as insulating the injection barrel and increasing the number of shots per machine cycle. This will reduce the amount of energy used per unit and lower your overall manufacturing costs.
Another way to improve energy efficiency in plastic injection molding is by minimizing shear and sprue forces. These forces occur when resin layers contact each other during the injection molding process. Fortunately, this can be prevented with careful design. For example, you can use a two-piece mold or make your part in small sections. In addition, you can choose a soft, flexible material that is less likely to break or crack.
You can also minimize energy usage by reducing the thickness of your plastics. This will reduce the energy needed to melt them, and it will also reduce the amount of pressure on the injected material. Additionally, you can use a multi-shot injection molding process to create multiple products in one machine cycle. This will save you time and money by reducing the number of machines required.
A reliable custom plastic injection mold manufacturer will provide you with a quote that includes all costs associated with the project, from tooling to finishing and assembly. This ensures that you are getting a fair price and avoids hidden fees. In addition, you should request quotes from multiple manufacturers to find the best one for your needs. If possible, try to avoid companies that have a minimum order quantity or require upfront payment for the entire project. This will prevent you from overspending on your project.
Cost-effectiveness
Achieving cost-effectiveness in injection molding is a complex process that requires careful design, material selection, and optimization of production processes. By emphasizing simplicity, efficiency, and optimization, manufacturers can reduce manufacturing costs without sacrificing quality or performance standards.
One of the most important factors in cost-effectiveness is choosing the right plastic material for the product. Different plastic materials have varying properties, performance characteristics, and price points. Choosing the most cost-effective plastic can significantly lower production costs. Commodity plastics like polypropylene and polyethylene are less expensive than engineering plastics such as polycarbonate and acrylonitrile butadiene styrene (ABS).
Another factor is the tooling costs, which are a fixed cost that increases with production volume. Minimizing cycle times and using multi-cavity molds can reduce these costs. Optimizing cooling channel designs can also improve cycle times and part quality. Another way to reduce costs is to re-use molds for multiple production runs, which can help spread the initial cost over many units and lower per-part production costs.
The quality of the injection molding equipment is also a critical factor. Low-quality companies use slow, old machinery that produces subpar results, while high-quality suppliers use modern, fast machines that produce accurate parts in a timely manner. A high-quality supplier can save you money by providing a more efficient and accurate product, and can prevent costly errors in production.
Labor costs are another significant factor in the cost of injection molded parts. Depending on the complexity of the part and the number of post-molding operations required, these additional steps can add up to a significant cost. By minimizing the number of post-molding processes, manufacturers can reduce their labor costs and increase production speeds.
When choosing an injection mold manufacturer, it is important to choose a company that has experience working with the type of plastic you need. In addition, be sure to inquire about the company’s quality and production capabilities. A good injection molding company will have high-quality machinery that is well-maintained and can meet your production needs. If you have a specific budget in mind, be sure to discuss it with your potential supplier.
Quality control
Plastic injection molding requires a lot of precision, and quality control procedures are vital to ensure that finished products meet high standards. These procedures can also improve productivity and lower production costs. Identifying flaws and ensuring that the product meets its intended function can help protect a company’s reputation and increase customer satisfaction. A quality control team can use various methods to inspect the finished product, including visual inspection, measurement, and functional testing.
Choosing the right material for your product is an important part of the quality control process. There are several factors to consider, such as chemical compatibility, thermal properties, and regulatory compliance. In addition, the choice of a plastic injection molder is an important consideration for project success. The company’s experience and expertise will determine whether it can produce your product in a short amount of time.
A plastic injection molder with a wide range of machines can handle different types of projects. Longer production runs require durable molds made of steel, while shorter production runs may use less expensive materials to save on tooling costs. The company should be able to provide detailed information about the molding process, such as how much pressure is needed to keep the mold closed while the injection is taking place.
Another important step in the quality control process is examining a plastic injection mold’s surface for defects, such as scratches or bubbles. This can be done using various methods, including computer tomography (CT). A CT scan can detect internal surface problems and reveal areas of poor ejection. This can reduce scrap rates, rework, and other costly mistakes.
An effective quality control process is essential for any manufacturing business. Properly inspected products can help prevent a company’s reputation from being damaged, and it can also prevent the need for costly rework or customer complaints. In addition, it can help reduce costs by reducing waste and improving efficiency.
While quality controls can’t eliminate all errors, they can significantly reduce them. In addition, the streamlined process allows companies to deliver quality parts quickly and cost-effectively. A quality control team can monitor the entire manufacturing process, ensuring that all components are manufactured to the highest possible standards. Injection molding manufacturers can use advanced software to anticipate potential defects before they occur. This can help reduce the time to market and ensure that the finished product meets the client’s expectations.